Connecting Doubly Fed Induction Generators to the Grid
Using an optimal crowbarless solution
Wind power penetration into the power generation system has substantially increased during the last twenty years, making the power quality and stability of this generation system increasingly important. Consequently, the grid codes, which establish the requirements all generation systems must fulfill in order to be allowed to connect to the grid, have been updated in order to guarantee the stability of the grid.
In recent years, wind turbines were allowed to disconnect from the grid when transients in grid voltage could jeopardize the integrity of their elements, especially the power converter. However, nowadays, due to the large amount of wind power installed in the generation system, this is no longer allowed. With such increase in installed power, the wind industry now faces the challenge of the suitable integration of the wind turbine into the grid, which main issues are the following:
Large distances between generation and load points
In many occasions, the areas with suitable wind resources are not close to those areas where the energy is being consumed. Series and parallel compensation solutions are installed in order to increase the capacity of long transmission lines. These systems can present issues related to Sub-Synchronous Resonances (SSR) and Sub-Synchronous Control Interaction (SSCI), among others.
Low capacity of the transmission lines
These grids are the so-called weak grids. They have a low Short Circuit Ratio (SCR) that in a wind farm is the relation between the short circuit capacity of the grid at the common coupling point and the rated power capacity of the wind farm. Basically, these are grids in which the voltage fluctuates with Active and Reactive power flow.
Fault Ride Through events
These events are usually caused by short circuits produced in the grid. Generation systems must be able to remain connected during these events in order to support the grid stability.
The Doubly Fed Induction Generator (DFIG) topology has proven to be an efficient and cost-competitive topology for wind turbines rated up to 3.5MW. Therefore, being currently the most installed topology.
However, its low grid integration capability jeopardizes the use of this type of conversion system, due to its high sensitivity to grid voltage transient, in which high voltages and currents appear in the rotor side of the generator, endangering the power converter connected to it. This is because the induction generator is directly connected to the grid, so any fluctuation in grid voltage produces a change in the generator flux, causing high rotor voltages and currents.
The most widely used system to protect the power converter under these events is the so-called active crowbar, a shunt circuit composed of actively controlled switches and dissipation elements which are connected in order to shunt the high currents, avoiding damages to the converter. This system, however, presents the limitation that while the active crowbar is connected, the power converter is not in operation, the active and reactive power set points cannot be tracked, and therefore the wind turbine is not being controlled.
This power converter is designed to operate in DFIG topology, not including an active Crowbar, but a Modular FRT system instead. In addition, the Modular FRT system is an optimal solution, which means that depending on the grid code to be fulfilled and the electrical characteristics of the system, especially the stator configuration, the Modular FRT system is selected allowing for a cost-optimal power converter for each wind farm scenario.
The Crowbarless solution presents advantages in the behavior when compared to the active crowbar system solution, especially in issues related to weak grids and FRT events. Moreover, these two events may occur together, being a major problem of weak grids. This takes place when a short circuit is produced in the grid and the protection elements upstream the fault trips, isolating different generator systems from the transmission system. Thus, rapidly changing the SCR in the wind farm (high d(SCR)/dt), making it difficult to control the voltage in the grid and therefore keeping the wind farm generators connected.
Voltage control in wind farms are usually tuned for strong grids, making the control dynamics not suitable for weak grids. The voltage control is not able to keep the grid voltage within the voltage range of the generation systems, as a weak grid presents high ratios of dV/dQ.
In DFIG topologies with converters including any kind of Active Crowbar system, this item is connected when the voltage transients in the grid causes rotor current or/and voltage values out the limit values of the converter. This can lead to instability of the Active and Reactive Power loops, and finally producing a disconnection of the wind turbine.
However, the Crowbarless solution, together with a suitable selection of grid filter and control loops tuning, is able to keep the control of the wind turbine during these transients, achieving the controllability required in order to operate in weak grids.
In addition, the modularity concept of the FRT system allows for a cost optimization for each application. The following figures show the behavior of the Crowbarless system under different grid events:
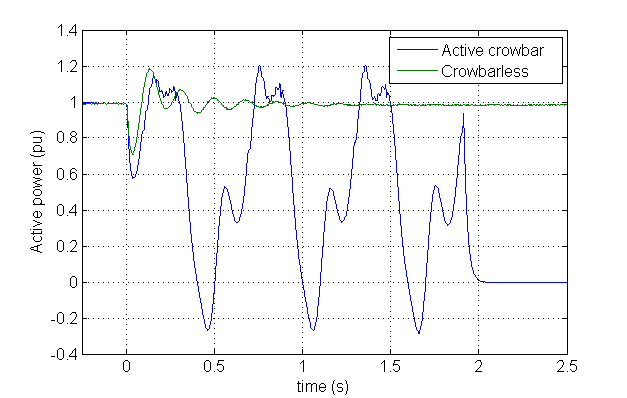
Figure 1 shows a comparison in the behavior of the Crowbarless system and the Active Crowbar system during a Short Circuit Ratio change from a value of 5 to a value of 2. It can be seen how the Active Crowbar is repeatedly activated leading to the instability of the system and finally getting tripped. However, the Crowbarless system is able to keep the control of the wind turbine, supporting the grid when required.
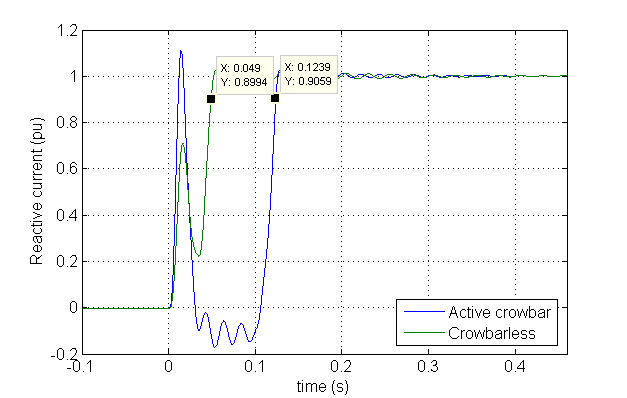
Figure 2 shows a comparison of the behavior of the Crowbarless system in a 20% 3-Phase Voltage Dip with a 3 MW Wind Turbine and rotor peak current of 11 kA in short circuit. The feed-in time of the required amount of reactive current is less than 50ms.
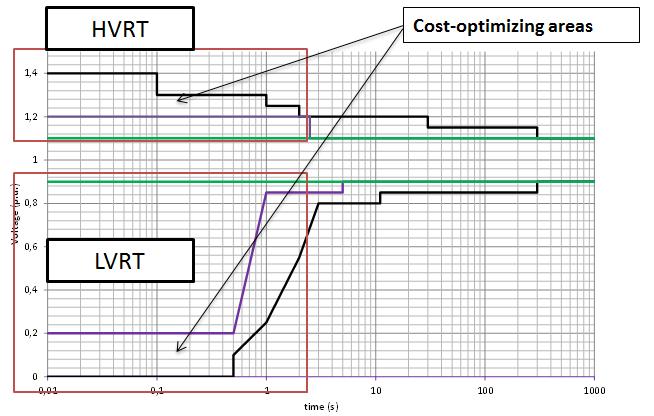
Figure 3 shows different grid codes voltage-time envelope requirements, highlighting the cost-optimizing areas for the Modular FRT system modular solution.

Figure 4 shows the Power Converter that includes the Crowbarless modular solution.
Aritz Lorea is the DFIG product manager for Ingeteam Power Technology’s wind business. The expertise of Ingeteam on this matter has been recognized by the American Wind Energy Association (AWEA), the national trade association for the US wind industry.
Ingeteam | www.ingeteam.com
Volume: 2016 May/June