Life Time Extension
How to maximize the return on investment
For a long time the wind industry has generated profit through manufacturing and project development. Once commissioning is achieved, the value must be kept or, if possible, increased. But what will happen to wind turbines that will soon reach the end of their design life?
There are a large number of wind turbines operating globally. By the end of 2014, there was an installed capacity of approximately 370GW, compared to 159GW at the end of 2009. Thus, for at least 43 percent of the fleet, life time extension (LTE) will be applicable soon, with predicted strong growth as all wind turbines will eventually reach the end of their design life.
Extending the operation of a wind turbine equates to increased revenue, which is gaining significant importance in the established wind installation markets. LTE also incorporates potential challenges that may lead to higher O&M costs and an increased risk of structural failures, which are more likely associated with additional cost, also considering the corresponding safety risks. On the contrary, the alternative is to decommission the turbine at the end of its design life, which will not deliver additional financial returns.
Theoretically, any wind turbine can be operated for an unlimited period of time if adequate maintenance is provided, even beyond its assumed life time of 20 years. One example for extending the normal design life is to replace damaged components. Armed with the most expertise about “Remaining Useful Life” (RUL), engineers apply detailed cost modeling to develop and evaluate a range of different lifecycle strategies.
The immediate benefits include
- Optimize Asset IRR: detect site-specific turbine component lifecycle, identifying long-term value of the asset;
- Optimize Project Financing: reduce risk in the financing or re-financing process, allowing longer and more comfortable debt return periods with less risk for the financing entity;
- Identify Weak Components: detect the weak component and adjust maintenance, reducing the costs of O&M;
- Optimize Operation: evaluate if an investment in maintenance / retrofits / load optimized operations will have an adequate return, detecting the risk of failure for other main components;
- Extend Cash Flow: extend turbine life based on turbine and site-specific conditions, maximizing the long-term value of the asset.
Currently there are two methods applied within the industry to calculate the RUL: analytical and/or practical.
The analytical component is to calculate the RUL with the aid of mathematical models. This mathematical analysis can be based on completely new calculations or by updating an existing calculation done in the past. By applying this method the RUL of a wind turbine is calculated after the actual damage has been established. New or additional calculations for the wind turbine are made, taking into account site-specific boundary conditions, such as wind loads. The structural integrity of a certain turbine is verified for extreme and fatigue loads. The output of this approach will be an expert statement with a stipulation of RUL.
The practical component takes the form of on-site inspection of the relevant wind turbines. These inspections are recommended to be done by an accredited company according to ISO/IEC Standard 17020. The focus of these inspections is to verify the output from the analytical part and proofs on the basis of the actual conditions on the wind turbines under consideration.
Based on the results of the analytical and practical components, it is possible to make statements about any potential RUL and/or about the inspection interval to be complied with. However, this analysis needs to be conducted with regard to aspects of structural safety.
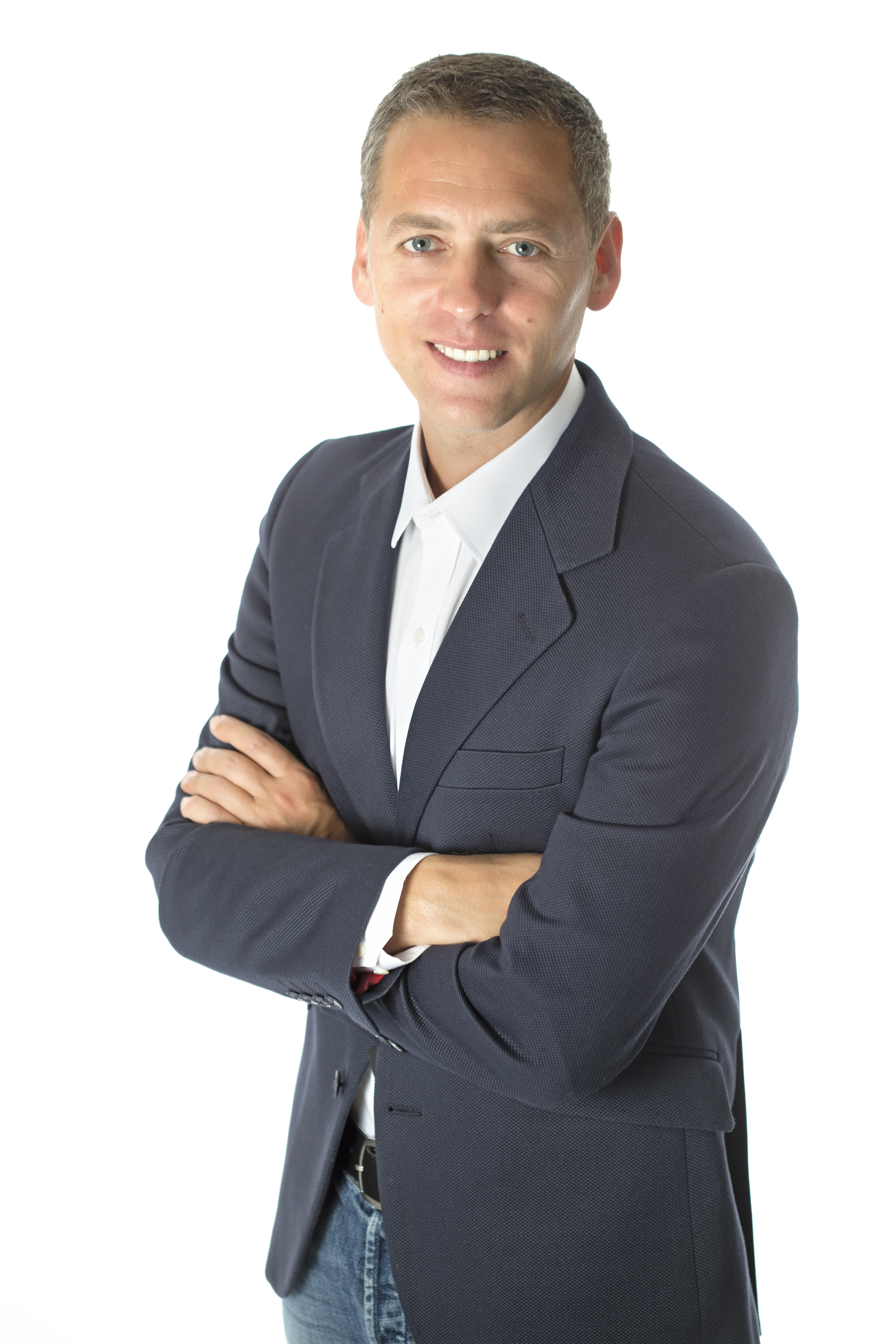
UL | www.ul.com/wind
Volume: 2016 May/June