Wind Plant Modeling Data Essential to Interconnections
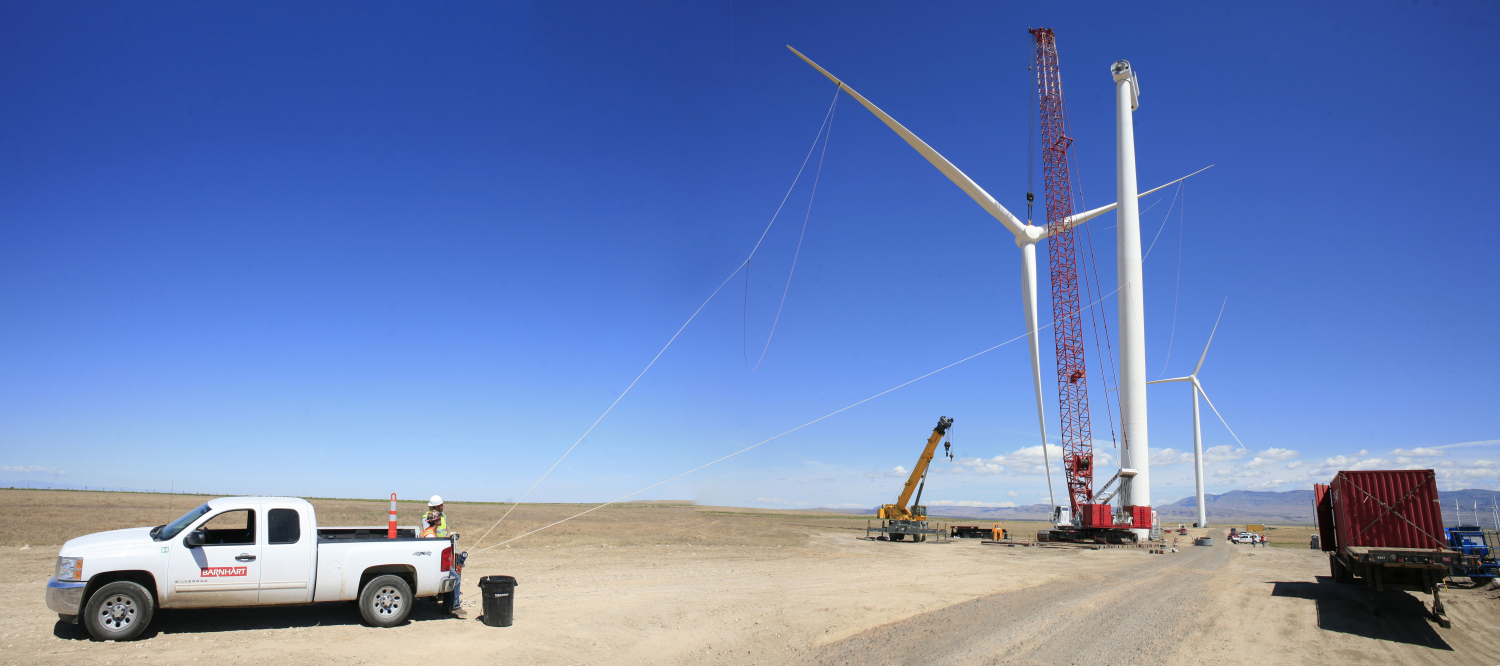
The North American Electric Reliability Corporation (NERC) requires generation operators to provide computer models when they apply to connect to a transmission grid in the United States or Canada. NERC requires verified modeling data whether the generation is conventional or renewable above a certain MVA threshold, which varies between interconnections.
The purpose of this modeling data is to study how the proposed generation will impact the grid now and in the future. The data also is used to compile detailed models of the grid to study how the system, as a whole, will perform for various disturbances that may arise.
The modeling discussed here refers to positive sequence models of the power system, which assumes that each of the three phases are balanced so only the positive sequence representation of the system is needed.
Positive sequence computer models for generators have two parts. This is true for conventional, wind, or solar photovoltaic plants. The first part is the load-flow or power-flow model. This is a steady-state or static model and represents the real power (MW) and reactive power (MVAR) capability of the generator.
In most cases, the load-flow model of a wind plant is fairly similar to the load-flow model of a conventional generator, except in the area of reactive power control. Most conventional generators generate reactive power (vars) to control the voltage of its terminal bus or some nearby local bus. Another difference with wind plants is the collector system for the plant is generally replaced with a calculated equivalent in the model so the model resembles a single generator with a step up transformer and equivalent tie line connecting to the utility point of interconnection.
Wind plants most often do not control voltage. Instead, they generate vars based on a constant var output control or a constant power factor control. Some larger wind plants, or solar plants, may be required to control voltage. In such cases, they are required to operate more like a conventional generator. Generally, this is only required when the interconnection point of the wind plant has poor voltage characteristics and the voltage control is needed to correct it.
The second part of a generator model, whether conventional or renewable, is the dynamic portion of the model, sometimes referred to as the stability model. Software packages simulating the positive sequence dynamic behavior of power systems will also include a load-flow module.
The load flow is used as the starting point for dynamic simulations. The load-flow program calculates how the power injected by the new generation will flow through transformers and transmission system, and eventually make its way to customer loads.
The dynamics simulation looks at how the generation responds to disturbances in the system such as faults and loss of a transmission line or transformer. System disturbances can cause generators to lose synchronism and can be very damaging to equipment.
System disturbances also can cause voltage fluctuations on the system. This can interfere with proper power delivery to loads, so determining how the new generation will affect the voltage profile before and after a disturbance is another important consideration in the evaluation of newly proposed generation. With wind turbines, the voltage and frequency ride-through characteristics of the plant are an important part of the dynamic model.
When modeling wind turbine dynamics, one of the biggest differences compared to conventional generators is the inertia of the machine. A conventional generator is electro-mechanically coupled to the grid through its inertia, and the mass of the generator is accelerated and decelerated with even the slightest change in frequency.
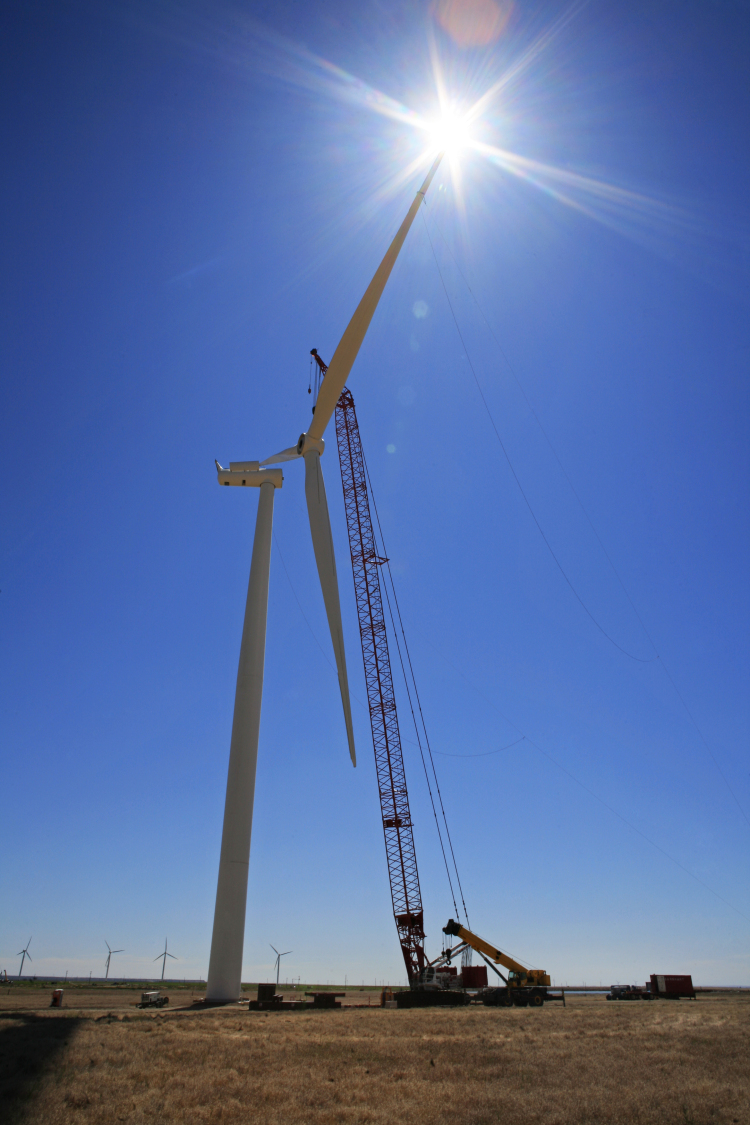
Type 1: fixed speed induction machine
Type 2: variable slip induction machine
Type 3: doubly fed induction generator or DFIG
Type 4: inverter-based generator, which injects power into the AC grid electronically
Types 1 to 3 all have significant inertia, although less than a conventional generator. Type 4 wind turbines, the most common generator currently being installed, has no inertia. Having no inertia, these are electronically coupled to the AC grid and not electro-mechanically coupled.
Having no inertia has some benefits, but also some disadvantages. One main benefit is inverter-based generation is much less susceptible to stability problems where the generator loses synchronism with the grid. Inverter-based generation only has to change its firing angle electronically to remain synchronized. Unlike a conventional generator, there is no accelerating or decelerating a rotating mass. A disadvantage in a system containing low inertia is frequency deviations caused by disturbances can be more severe.
Whenever new generation is being proposed, the interconnecting utility is required to do some simulation studies to make sure the proposed generation will operate as expected under normal conditions and will also operate acceptably under abnormal conditions.
Power systems are very complex and expensive, and simulations are the easiest way to evaluate how these systems are going to interact. After things are built, it is too late to find out they are not going to play well together.
Sometimes wind developers will want to run their own simulation analysis of a planned interconnection to see if their plans have any obvious issues before submitting the interconnection application. This can be useful for determining a suitable generation size and interconnection voltage level prior to the application process. This can help speed up the application process by avoiding a proposed interconnection that will run into complications in the utility system impact study.
Recently, most utilities have spent considerable effort to improve their data and validate their generator models. This includes testing of generators or recording of system disturbance events to obtain field validation of the model parameters. NERC MOD-025-2, which requires verification and reporting of generator real and reactive power capability, applies to wind turbines and is phased-in over five years with at least 40 percent of each generator owner’s units due by July 2016.
Field validation of generator excitation dynamics or equivalent controls, and turbine-governor dynamics or equivalent became effective in July 2014 for new or changed plants or controls. For existing plants, the compliance is phased-in over 10 years with at least 30 percent of each generator owner’s MVA due by July 2018.
The most common software packages used in the United States for simulating large scale positive sequence models of power systems are PSSE by Siemens-PTI, PSLF by General Electric and PowerWorld by PowerWorld Corporation.
All of these packages contain many of the same standard models for different types of equipment including generators, transmission lines, transformers, shunt reactive devices, loads, and relays.
A typical power system model of the western United States is going to contain many thousands of each of these components, so there is a substantial effort that goes into developing a database to represent the system for different numbers of years projected into the future and different seasons of the year.
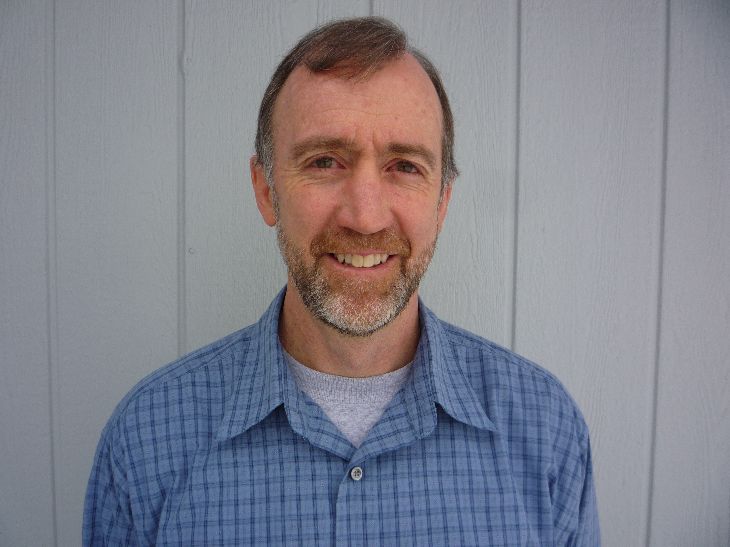
Power Engineers, Inc. | www.powerenergineers.com
Volume: 2016 March/April