Potential and Limitations in Large Wind Turbine Blades - Sweep- and laminate-induced torsion coupling
Wind turbine ratings are increasing and trending towards larger MW scaled rotors for lower wind class sites. Although rotors are getting larger in size, they must still be designed for root load targets which produce a favorable cost in energy savings. The load reduction for larger machines is obtained through both conventional and advanced methods. Conventional methods typically include incorporation of pitch regulation along with advanced control systems, however, high pitch rates can increase fatigue loads and reduce the life of the system. Advanced methods include incorporating aeroelastic tailoring techniques along with advanced control techniques. Aeroelastic tailoring of wind turbine blades to reduce transient loads is not a new concept and the fundamental basis for aeroelastic tailoring is to design the blade so it undergoes an out-of-plane flapwise deflection and twist during operation. This torsional deformation is known as Torsion-Bending Coupling (TBC).
The advantage of TBC happens when a blade is hit by a wind gust or transient wind condition. The downwind flapwise deflection of the blade caused by the gust induces the blade to twist so it changes the aerodynamic angle of attack and reduces its aerodynamic loading.
This technology reduces the cost of energy (COE) by increasing the annual energy production (AEP) of the wind turbine by allowing larger rotor blades to be used without a significant increase in the turbine system loads. Studies show load reductions through the use of TBC are 8% to 12%. Reductions in COE of approximately 8% are achievable and the use of larger rotor blades for as much as 16-20% increased energy capture offset the increased rotor blade cost. While most of the early work on aeroelastic tailoring focused on the dynamics and impacts of loads and energy capture, later studies focused on the optimal off-axis fiber placement in order to maximize the magnitude of twist-flap coupling. Additional studies focused on the structural details of various blade designs to achieve twist-flap coupling.
Laminate induced TBC
Aeroelastic tailoring, through the rotation of some of the fibers in a laminated fiber-reinforced composite structure away from the spanwise direction (the long axis of the blade), induces a torsion-flap coupling in the structure. In this approach, the resulting laminated composite structure must be unbalanced, and fibers placed at an angle θ, relative to the long, spanwise axis of the blade cannot be balanced by an equal weight of the same fibers at an angle of –θ. The presence of this unbalanced structure creates a coupling between axial tension and compression in the structure (parallel to the long axis) forcing in-plane shear and deformation. The net resultant deformation will induce the blade to deform torsionally and twist about its long axis.
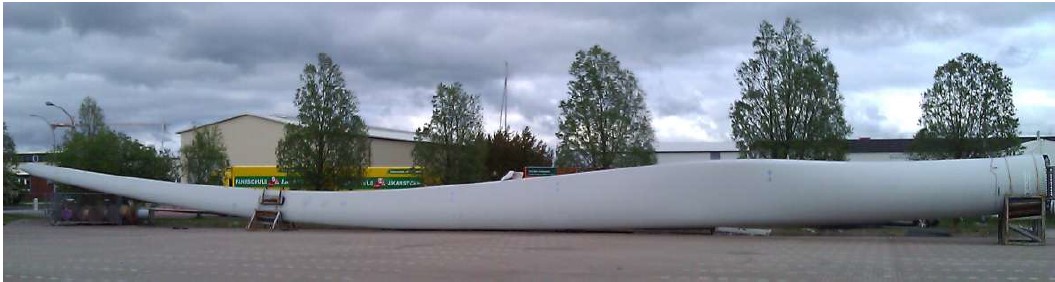
Blade sweep refers to geometrically modifying the shape of the wind turbine blade to achieve loads reduction due to aeroelastic tailoring. This is achieved by geometrically sweeping the outboard-region of the blade in the plane of rotation aft of the pitch axis. The loads generated at the tip will introduce a moment about the pitch axis. Since the blade incorporates sufficient torsional flexibility, the tip will twist towards feather. This ‘swept’ shape allows the blade to respond to turbulent wind gusts through a process of controlled twisting and bending. As the blade twists, it sheds loads and material stresses which would normally be translated to the root of the blade.
It is estimated 4°-7° of tip twist is required to obtain an 8-12% reduction in blade root loading. Image 1 shows a swept blade.
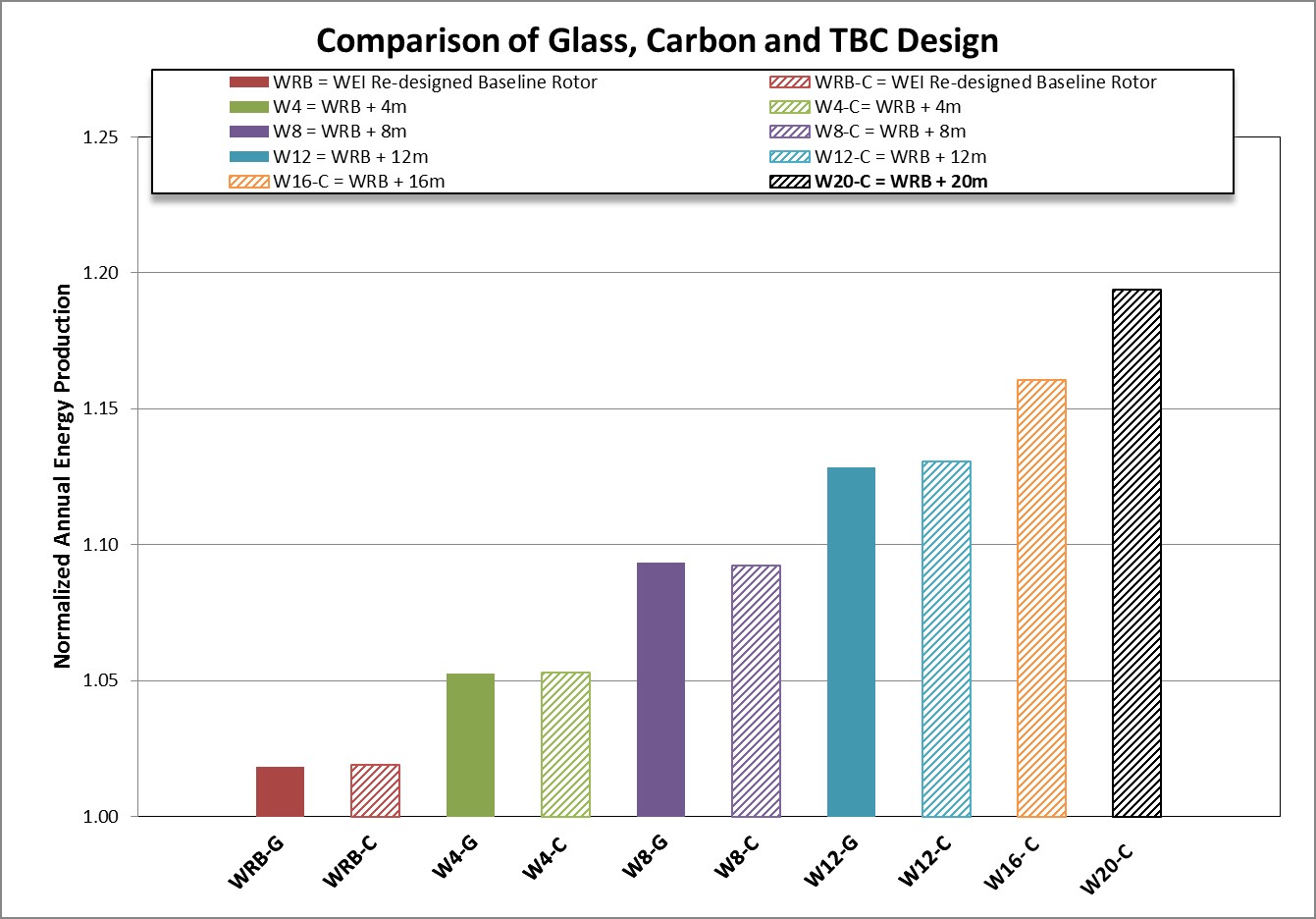
TBC is an enabling technology when designing large wind turbine blades. Often, the challenge is to seek the largest rotor diameter for a given turbine rating. A performance and cost analysis should be performed to compare different rotor sizes based on different material configurations. The load target for some rotor configurations is provided in Figure 1 which shows increases in AEP of approximately 19% for the largest rotor configuration incorporating TBC either with off-axis laminates or geometric sweep. Note this is 6% higher than the largest rotor which does not incorporate TBC, as it only achieves an estimated 13%.
Another benefit of laminate induced TBC is its simplistic manufacturing with off-axis carbon though stitch bonding. Unlike geometrically swept rotor blades, laminate induced TBC can be incorporated in blades with conventional profiles. This reduces manufacturing cost and complexity for large blades. For swept blades, custom designed fabrics are not required, which reduces the lead time for manufacturing.
Limitations of TBC
- Although TBC is an enabling technology for large wind turbine blades, there are a few limitations associated with it. Custom fabrics (carbon glass hybrid) required for the shell material of laminate induced TBC blades are more expensive than conventional triaxial glass material.
- Manufacturing individual components for swept blades can be complicated; fabrication of the girder requires the use of prepreg material.
- Swept blades are difficult to transport which increases transportation cost and time.
- Due to the curvature in the swept blade profile, an external torque load is generated which can be transferred through the pitch system.
- Although a reduction in total cost of energy is obtained, it increases blade cost. It should be noted, for large offshore machines, the total blade cost accounts for only a small fraction (~10%) of the total system cost.
The use of TBC in large blades results in reduction of blade root loads which, in turn, enables the design of larger, more energy efficient rotors. The load reduction obtained from TBC is estimated to be 8-12% of the uncoupled blade root loads. A TBC blade presents itself with a few limitations; the overall blade cost is higher than a conventional blade design, and there are manufacturing complexities relating to either custom fabric production for a laminate induced TBC or the manufacturing of the swept blade contour, but these obstacles are usually diminished by the gains in overall system life cycle.
Mr. A. A. Raina is managing director, Dr. K.K. Wetzel is CEO/CTO, and Mr. K. T. Lee is technical project management & business development manager, wind at Wetzel Engineering Inc.
Wetzel Engineering, Inc. | www.wetzelengineering.com
Volume: January/February 2016