Putting Waste to Work
Developing a more efficient way to produce biofuels

When Munch began working on his Master’s degree in engineering, he had his sights set on producing biodiesel. Fresh from an undergraduate degree in biochemistry, he was eager to apply his science background to the real world. The idea of using vegetable sources of biodiesel quickly caught his fancy. He was convinced it was the greatest idea since flux capacitators; it was the future, and he was going to be part of it. His enthusiasm ran into the hard wall of reality when he read this sentence: Increasing demand for vegetable-based biodiesel has caused an increase in food prices worldwide. He decided he didn’t want to contribute to the problem.
Munch wasn’t about to give up on his dream, though; he just had to find a different way to grow his biodiesel precursors. Enter a little-known yeast strain called Rhodosporidium diobovatum. Another student in his lab group had published a paper on the ability of different yeast strains to produce the fatty acids that serve as precursors to biofuels and it turned out the diobovatum was one of the high producers.
Munch wasted no time putting the strain to the test in Dr. Cicek’s lab. He soon found it had star quality: not only did it grow very fast and produce fatty acids in abundance, but it could metabolize a number of different carbon sources, one of them the glycerol recovered, ironically enough, from the sludge left over after producing biodiesel from vegetable oil.
The hard-working yeast strain also intrigued Munch’s project supervisor, University of Manitoba engineering professor, Dr. Nazim Cicek. Munch had proven the strain’s worth in a laboratory flask. But what kind of yield would it produce on a larger scale? In bottom-line terms, they wanted to scale up the process to find out if it had commercial potential, while allowing Munch to learn what post-treatment looks like.
Munch knew just where to turn. Some months earlier, he had attended a meeting where he met a student of Dr. Lars Rehmann, an assistant professor of chemical and biochemical engineering at the University of Western Ontario in London. As the two grad students chatted about their respective projects, Munch learned that Dr. Rehmann’s chief interest lay in optimizing bioreactor performance. As such, he had the equipment and expertise to pilot-test Munch’s bioprocess on a larger scale.
Training the future
This led to Munch applying for a BioFuelNet (BFN) exchange grant, which funded an eight-week stint in Dr. Rehmann's lab. Such grants are an integral part of BFN’s ongoing education and training program. Programs such as this, help train and launch a large number of young professionals, dubbed High Quality Personnel, who will develop the Canadian biofuels industry to its full extent.
The program provides R&D training, professional skills training, career development and networking opportunities, and funding for R&D initiatives within the academic, public, and private sectors in Canada, and beyond.
Student exchanges such as the one that brought Munch and Dr. Rehmann together seek to strengthen interactions within the biofuels community, transfer knowledge between labs, expose young professionals to different problem-solving approaches, and strengthen Canada’s exposure to the international biofuels scene.
The exchange bore ample fruit for Munch: Drawing on Dr. Rehmann’s experience and research facilities, he was able up his production scale to a 100-L pilot-scale reactor system. He breathed a sigh of relief when his yeast came through with flying colors, allowing for even bigger production tests.
Back to the drawing board
As it happens, “going bigger” isn’t as simple as using larger quantities of starting materials. When working with just a liter, the process can be straightforward, but as the system gets larger, the surface area-to-volume ratio changes, which makes it more challenging to get oxygen into the system. Moreover, using a larger impeller [the rotating component of a centrifugal pump] increases the shear stress on the yeast, which can lead to cell breakdown. In other words, it’s not given that a procedure which works in a beaker will also work in a bioreactor. That’s why it’s important to take small ideas and move them up to a semi-industrial scale.
The final step will be to determine whether the process has economic legs. This will depend on several factors, including the price of fossil fuels and the availability of industrial partners. The research group eventually plans to expand the project, to include other sources of waste to feed the yeast. Ideally, they can eventually link up with a biofuel production company which generates the waste the Prairie Platform uses as fuel. A win-win scenario if ever there was one.
Munch has recently accepted a PhD position in Dr. Rehmann’s lab where he will work on fine-tuning the growth conditions for his yeast strain in hopes of achieving even higher fatty acid yields.
Munch is right where he wants to be. He’s still growing fuel, just as he set out to do. The only difference is that his ‘labour force’ is microscopic. Munch says, “ I think it’s amazing that the waste I’m using in the process comes from biodiesel production itself. Talk about closing the loop!”
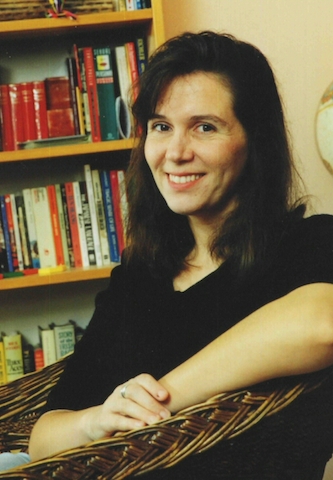
BiofuelNet Canada | www.biofuelnet.ca
Author: Gabrielle Bauer
Volume: July/August 2015