Taming the Cold - Turbine blades brave icing conditions
Within the North American wind energy industry, the challenges associated with climates characterized by low temperatures and icing conditions are widely acknowledged. As of the end of 2012, two-thirds of the 11.5 gigawatts (GW) of wind energy capacity installed globally in moderate to severe icing climates was located in Canada and the United States, compared to one third in Europe (according to the BTM World Market Update).
Furthermore, it is forecasted that 5.9 GW of North America’s added capacity by 2017 will be sited in moderate to severe icing climates.
Ice assessment
The presence of ice on a wind turbine blade, if significant enough, will affect its aerodynamics, which leads to lower energy yield (see Image 1). According to Lacroix (2012), an average of 7.5% of annual production was lost in Quebec in 2011 due to icing climate. The Quebec wind industry is, currently, deploying considerable effort to overcome various technological challenges related to wind plant operation in winter conditions.
In light of the most recent call for tenders in Quebec for a 450 MW wind power farm, many industry players agree that the upcoming contracts with Hydro-Québec will hinge on proper ice assessment. As a result, the industry is keen on having reliable icing maps and validated correlations between meteorological icing, instrumental icing, and production losses.
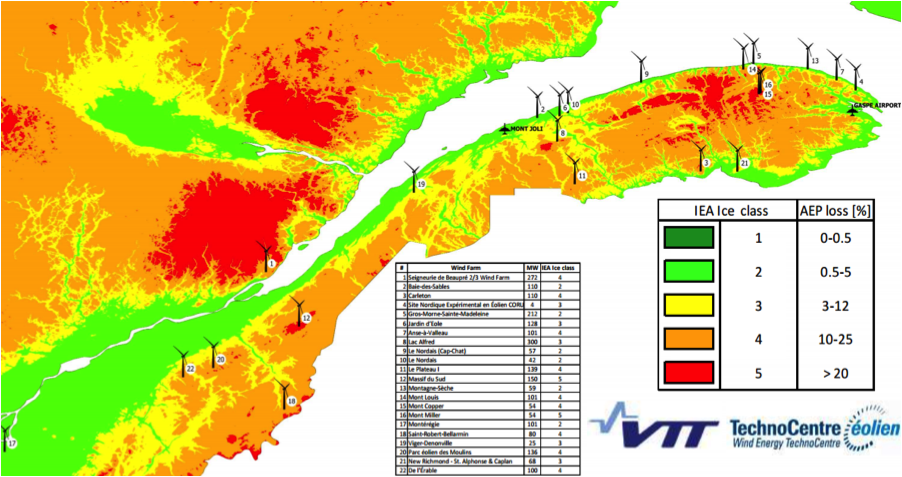
Ice protection systems
The wind industry has also identified a need for ice protection systems (IPS). Regardless of whether or not icing-related production losses have been estimated correctly during the assessment phase, IPS might be worth including. In fact, anytime icing occurs at a wind energy site, a potential business case can be made for the installation of IPS.
The idea behind an IPS is to recover all or part of the energy potentially lost due to icing by preventing ice accretion on the blades, or by shedding the ice from the blades (see Image 2).
IPS’ closest to technological maturity include hot-air and electro-thermal de-icing systems. Anti-ice coatings, though highly appealing due to their potential low-cost and low-maintenance requirements, still must prove their effectiveness and durability in the field. Retrofit options are much more limited for wind turbines in operation that aren’t already equipped with a built-in IPS. However, some independent service providers are proposing de-icing solutions using helicopters, rope access, or even robots.
The general consensus is that these systems still lack a proven track record and would benefit from standardized performance validation. Many developers would like to see performance warranties similar to those offered with a standard turbine.
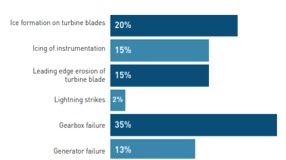
Operations and maintenance (O&M) during winter presents challenges and opportunities. In a survey conducted in 2014 by Wind Energy Update, over 100 respondents involved in the Canadian wind sector revealed that icing was the most significant cause of production loss, at par with gearbox issues (see Figure 2).
Energy yields are higher in the winter and, as a result, downtime is more costly during colder months. Furthermore, access time and costs are likely to be greater. Based on a case study, Boucher (2013) estimated that O&M activities can be 30% more expensive in the winter when considering increased energy yield, increased access costs, and increased technician time.
Signal trending or condition health monitoring can help predict failures, thereby reducing the costs of maintenance, particularly if the maintenance activities must be carried out during the winter.
To access their assets in winter, wind farm operators mainly rely on one of three methods:
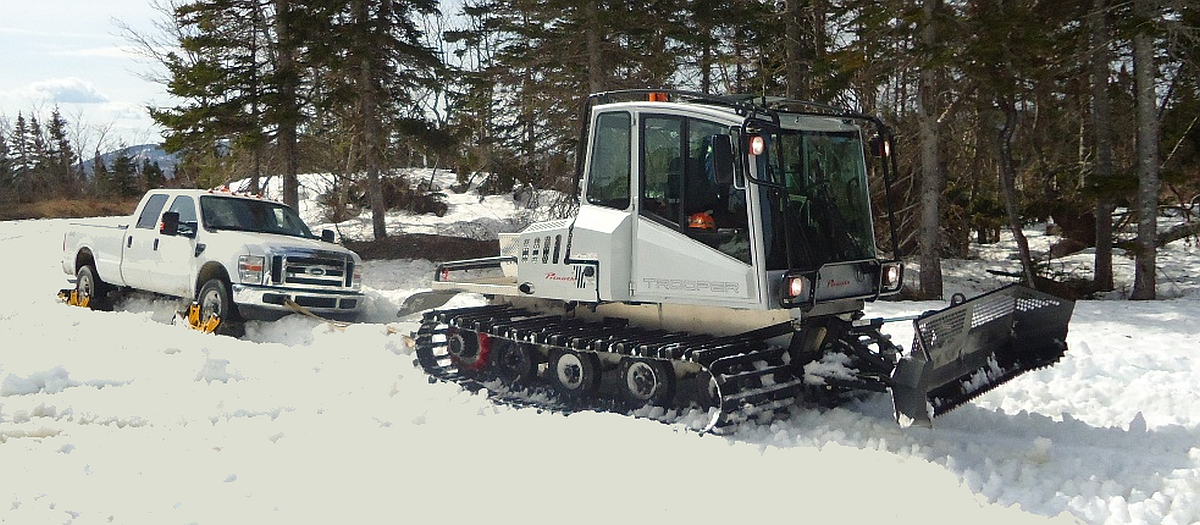
Employing vehicles specially adapted to drive in snow; or
Performing a minimum maintenance of the roads to allow for the use of four-wheel drive (4WD) pick-up trucks or ATVs on tracks.
Various factors, such as the amount of snow accumulation on site, as well as the layout of the wind turbines and access roads influence operators’ decisions in this regard.
A recent survey** of 11 wind farm operators throughout Canada revealed that the latter most often use vehicles adapted for winter conditions. Of those who don’t maintain access roads: 92% use snowcats (at an approximate cost of $200,000); 69% use snowmobiles (at a cost of $10,000 to $16,000); and 62% use 4WD pick-up trucks on tracks (at a cost of $15,000 to $25,000).
It should be noted that 85% of operators surveyed use more than one type of vehicle, and those who use 4WD pick-ups on tracks also have snowcats. None of the surveyed operators exclusively use snowmobiles.
The challenges brought upon by cold climates have raised the bar for OEMs, operators, and ISPs who have answered with innovation and resourcefulness. As a result, the wind industry is becoming stronger and more competitive than ever.
* Note: The VTT worked in collaboration with the TechnoCentre éolien (TCE) on this ice map as a joint partnership
** Survey conducted by the TechnoCentre éolien
The TechnoCentre éolien (TCE) is a center of expertise that supports the development of the wind industry through research, technology transfer, and technical assistance for businesses. The TCE’s primary areas of activity relate to wind energy in cold climates and complex terrain, adaptation of technologies, and integration of supply chains.
TechnoCentre éolien (TCE)
Author: Matthew Wadham-Gagnon, Caroline Farley & Bruno Boucher
Volume: March/April 2015